Our three-chamber HCC (horizontal continuous casting) furnaces are mostly used in the production of hollow shells, tubes, bars and wire rod. An HCC furnace consists of a refilling, a pressurized and a casting chamber. The three chambers are heated by an integrated sandwich inductor and the casting chamber is fitted with a flanged-on mould. Automatic pressure control in the middle chamber ensures that the bath level in the casting chamber is always constant.
The three-chamber design decouples metal refilling from the casting process. This makes it possible to have longer intervals between the transfers of molten metal from the melting plant. For the operator, this provides more production flexibility and reduces the investment costs.
Benefits at a glance:
- Optimal alloy quality
- Constant metallostatic pressure
- High casting speed
- Highly efficient strand cooling
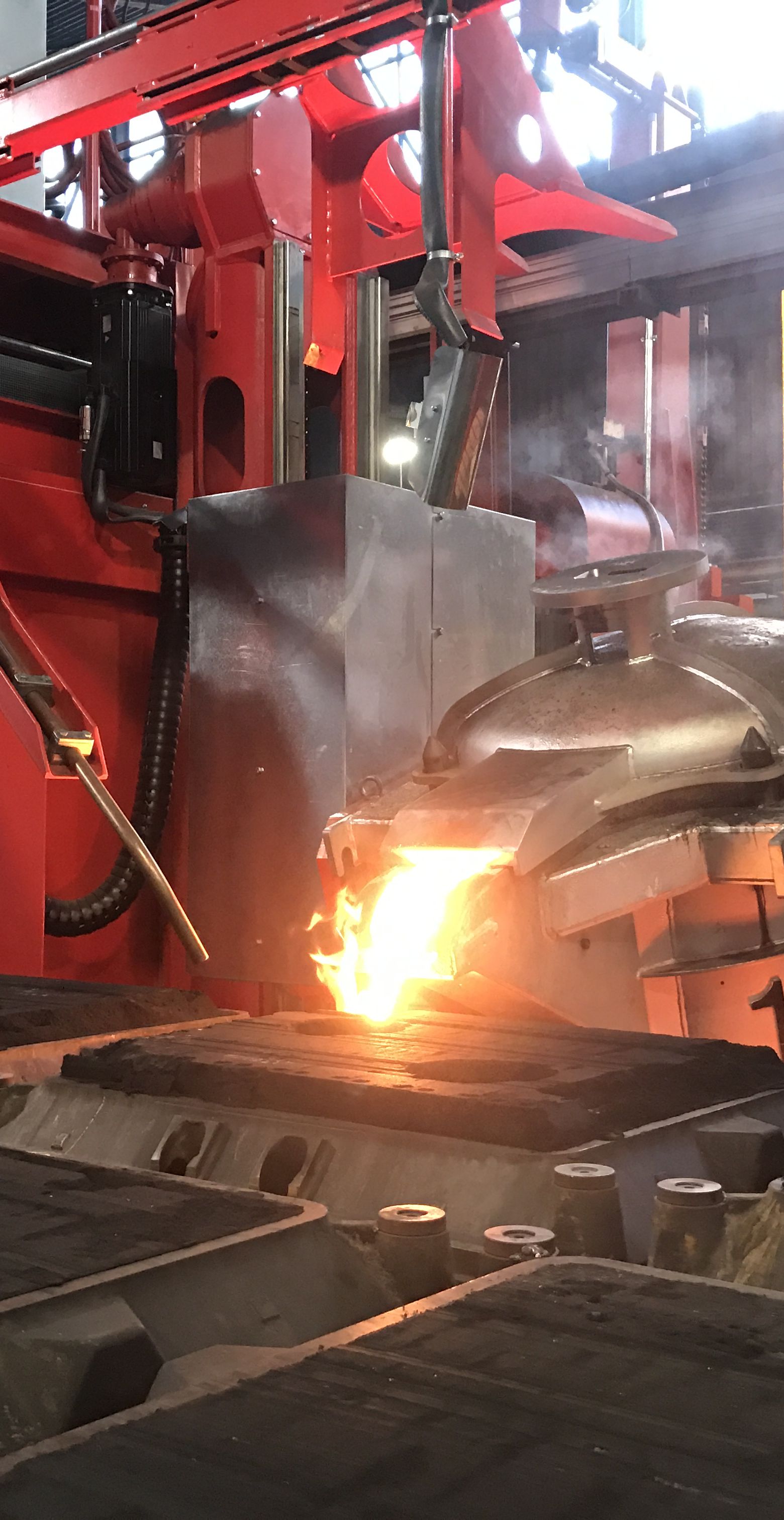
The bath level in the refilling chamber is kept at a constantly high level, resulting in a small fall height when new material is added. This guarantees optimal alloy quality.
The exact bath level control in the casting chamber ensures that the metallostatic pressure acting on the strand shell is constant at all times. The high pressure in the casting chamber enables high casting speeds.
The closed furnace design reduces metal oxidation and dross formation to an absolute minimum, achieving optimum material efficiency.
The flanged-fixed mould can be quickly and easily replaced.
We equip furnaces used for special-alloy casting with a crucible-type inductor as an option.
Metals | Copper and Brass |
Temeprature | Up to 1,250 °C |
Design | Pressurized three-chamber furnace (refilling, pressurized and casting chambers) and sandwich inductor |
Capacity | From 5.0 up to 35.0 t (with brass) |
Throughput | Up to 17 t/h |
Electrical power | From 150 up to 500 kW |
Downloads
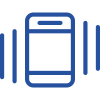
Phone +49 2473 601-710
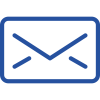
E-Mail info@induga.de