Ceramic-lined induction-heated dipping tanks are increasingly used in batch galvanizing because they help reduce CO2 and NOx emissions from hot-dip galvanizing processes. With Induga channel-type induction furnaces, the bath temperature can be precisely controlled within a wide range to achieve excellent coating results.
The higher bath temperatures attainable make it possible to achieve thinner coatings and comply with even tighter coating thickness tolerances. The enhanced adhesiveness of the coating results in reduced production costs and improves strip formability.
The plants are equipped with a high-precision bath level measuring system that sets the bath temperature with an accuracy of ± 2°C by automatically adjusting the inductor power.
Benefits at a glance:
- Precise control of the bath temperature
- Wide temperature range
- Good adhesion of the coating material
- Long life of the boiler
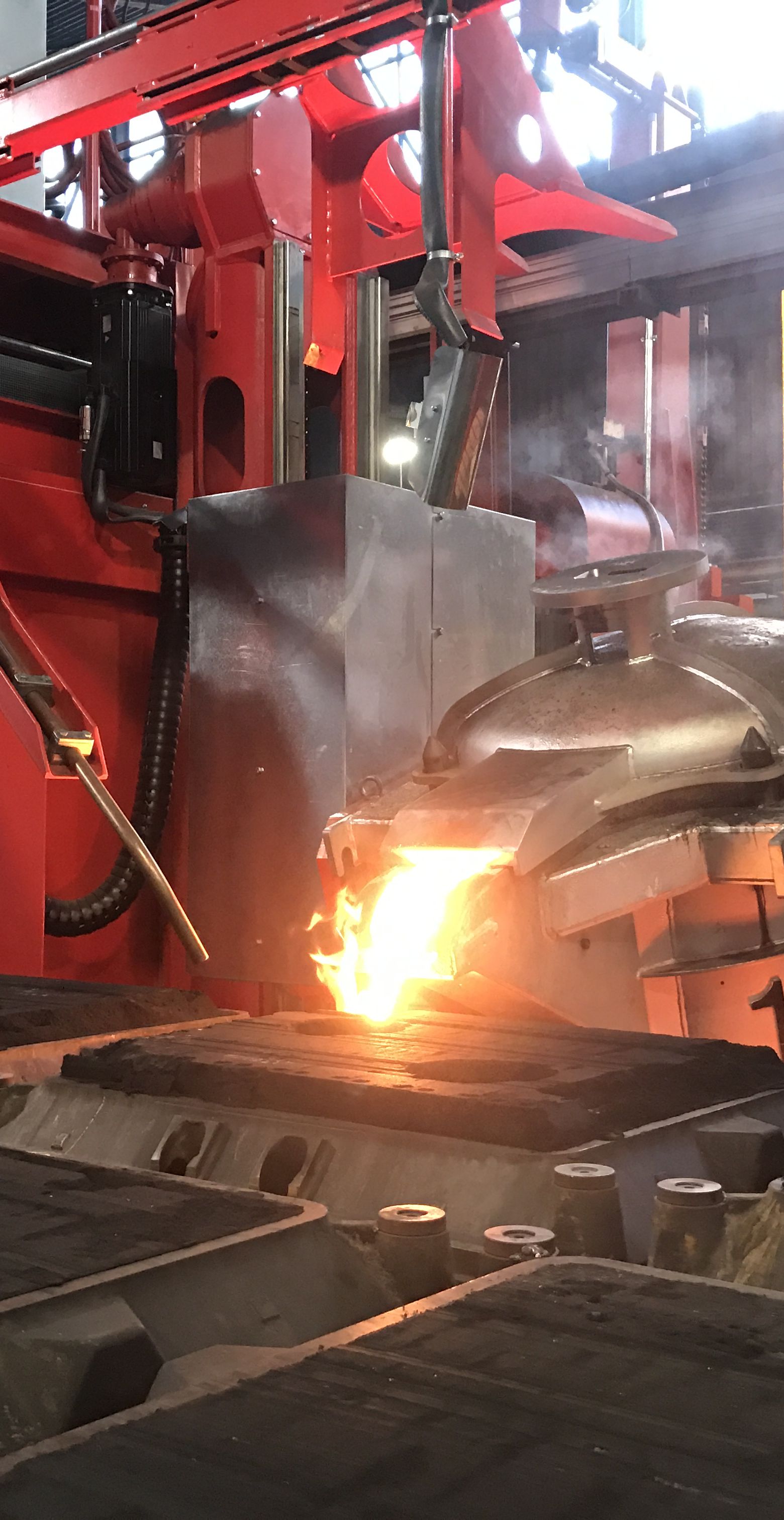
The ceramic lining of the coating pot guarantees a long service life and high availability of the equipment.
Separate pre-melting furnaces can be used to optimize the energy requirement of the process and enhance the thermal stability of the bath. Depending on the specific application, pre-melting units are designed as channel- or crucible-type induction furnaces.
Capacity | Up to 300 t |
Bath temperature | From 450 up to 650 °C, automatic control (± 2°C) |
Design | Channel-type induction furnace with ceramic lining |
Number of inductors | With single or several inductors |
Inductor capacity | Up to 650 kW (air or water cooling) |
Furnace capacity | From 200 up to 3,000 kW, depending on number of inductors |
Downloads
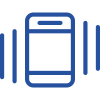
Phone +49 2473 601-710
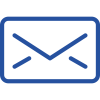
E-Mail info@induga.de