Ingots, non-ferrous metals scrap and bulky material are usually melted in channel-type induction furnaces because they operate at high electrothermal efficiency and can be designed to be virtually any shape. They offer high temperature stability and process security, even when charging ingots or other bulky material.
There is much less bath agitation than in crucible-type furnaces, keeping oxidation at the bath surface very low.
One or two channel-type inductors can be fitted to the hydraulically tiltable furnace vessel.
Channel-type induction furnaces feature long service lives, are very easy to clean and require only little maintenance. They combine low energy costs with economic, carbon-free melting.
It is possible to operate several channel furnaces in combination and adapt them to varying production conditions using flexible conveying and lifting systems.
Typical uses of channel-type induction furnaces include holding and pouring molten metals as well as continuous and batch-type coating processes.
Benefits at a glance:
- Flexible furnace geometry
- High electrothermal efficiency
- Controllable furnace atmosphere
- Low operating costs
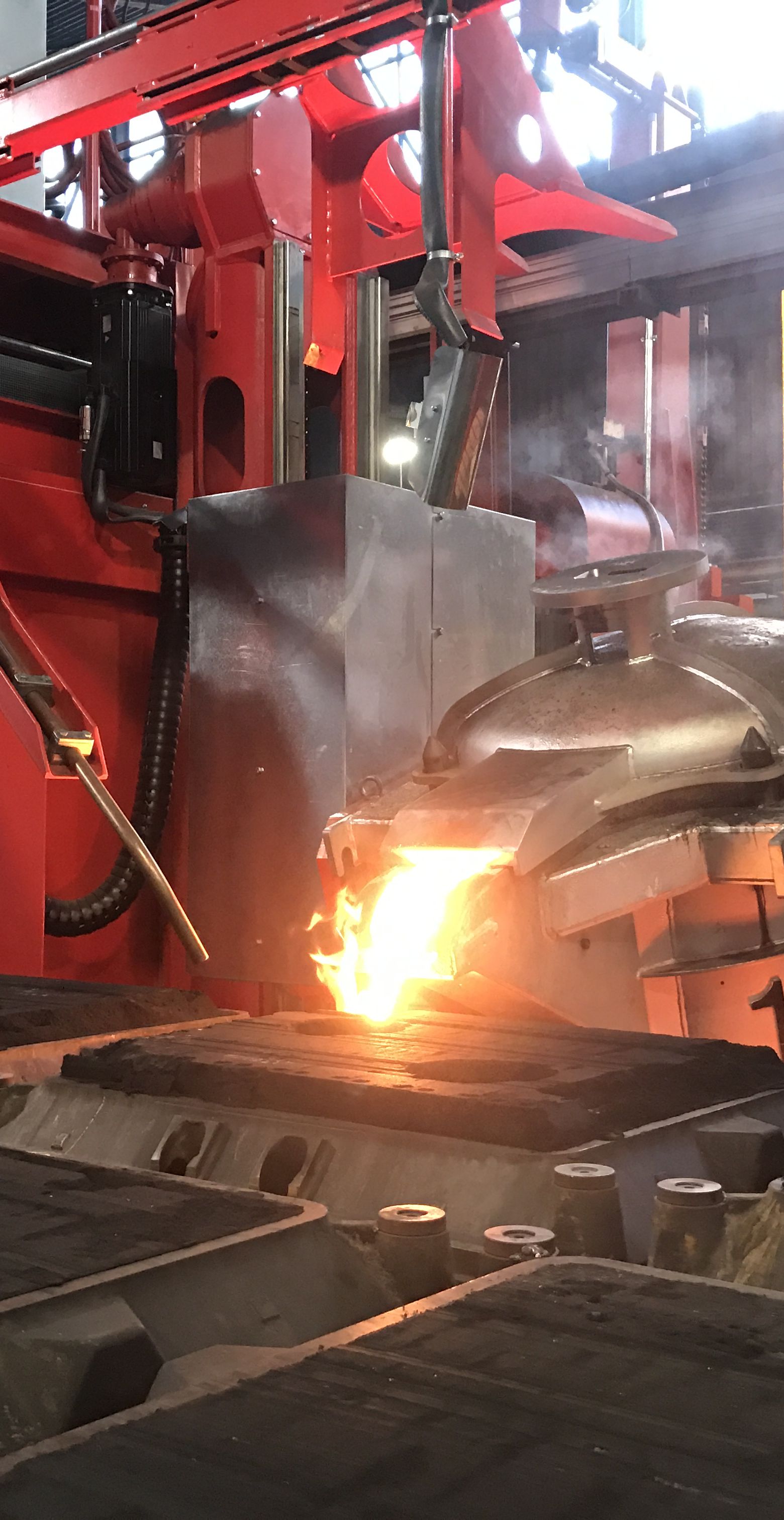
Channel-type furnaces: Ideal for continuous processes
A channel induction furnace is the perfect option for continuous melting and casting processes where the alloys are not frequently changed. They achieve efficiency rates between 80 and 90 percent.
The furnace vessel containing the metal bath can be cylindrical, trough- or drum-shaped. Multi-chamber vacuum furnaces can also be designed as induction channel furnaces.
Typical use | Non-ferrous metals melting |
Design | Channel fitted with one or two inductors |
Furnace type | Hydraulically tiltable |
Electrical power | From 250 up to 3,000 kW |
Capacity | From 1.0 up to 30.0 t |
Tapping mode | Batch-type |
Tap weight | From 0.6 up to 25 t |
Downloads
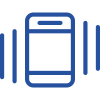
Phone +49 2473 601-710
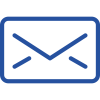
E-Mail info@induga.de