Our Puma Pro ladle pouring machines are successfully used in casting lines using flask, flask-less or chemically bonded moulds. Puma Pro pouring machine ensures efficient and safe pouring of iron, steel, stainless steel, aluminium and other non-ferrous metals alloys.
The Puma Pro pouring machine captures and processes all of the process-relevant parameters and integrates the pouring process into the foundry’s digital Industry 4.0 environment.
The unique, model-based predictive casting control system and the iterative casting optimization software ensure optimum material and energy use at minimum costs. In this way, Puma Pro pouring machine has a direct positive effect on a foundry’s productivity and profitability.
In combination with the accurate casting process control, the high-precision measuring technology optimizes utilization of the available melting capacity to ensure maximum material efficiency.
Benefits at a glance:
- Maximum yield achieved by high-precision control of the entire casting cycle
- High repeatability guaranteed by high degree of automation and exact pouring process control
- Low operating costs thanks to minimal energy requirement
- Flexible material use
- Direct increase in profitability and productivity for the foundry
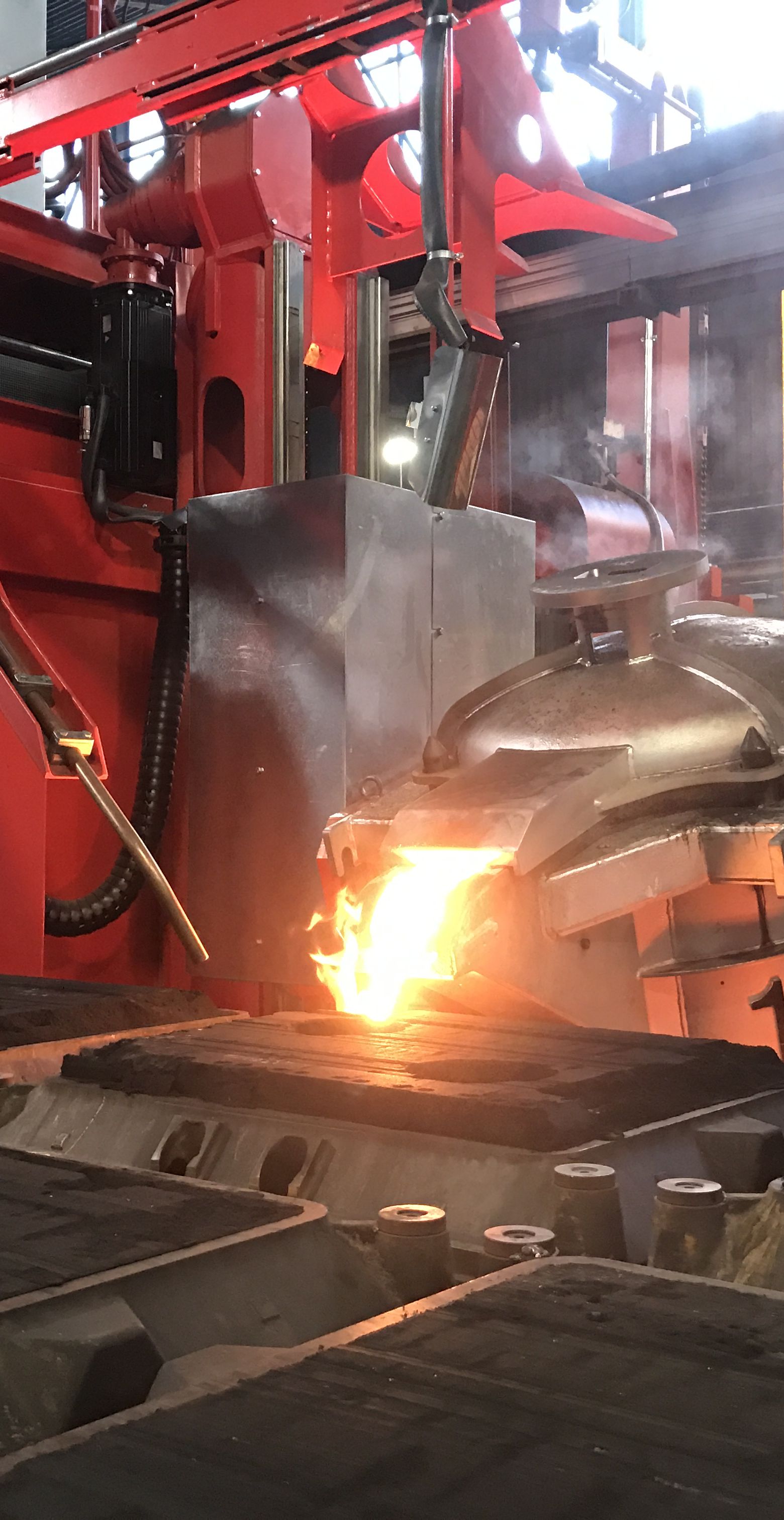
Precise process control
The pouring machines feature deep automation and precise control of the entire pouring cycle to ensure high repetition accuracy.
With its model- and parameter-based process control system that automatically retrieves the input values from a dedicated database, PUMA PRO pouring machine achieves the highest possible productivity at maximum flexibility. The system is able to generate a separate model for each individual mould, even if each ladle is filled with a different alloy.
The intelligent pouring control algorithm optimizes funnel filling and stops the pouring operation precisely at the point when the specified filling weight is reached. As a result of its iterative learning capacity, the system autonomously optimizes all subsequent pouring cycles, taking into account variations in parameters, such as sand moisture, and slag formation in the ladle. This results in minimized material use.
The operator can always see what is happening, how the pouring system is operating.

Stable temperature
The optimized shape and highly efficient insulation of the ladle keeps heat loss during metal pouring and transport extremely low, in many cases below 3°C per minute.

High availability
Puma Pro pouring machine is the only pouring machine of its kind on the market using the patented 2D pouring jet positioning system for optical process monitoring. This prevents metal spilling on the flasks or contaminating the casting line. So, Puma Pro pouring machine helps improve casting line availability, too.

Easy integration
The machine’s compact design facilitates its integration into existing casting lines. Foundations are not usually necessary. The three-axes ladle positioning system makes low pouring heights possible. Standard interfaces are provided to ensure smooth integration into the melting and casting processes, existing material transport systems, bath treatment processes and quality control.

Available options
The Induga twin-ladle pouring system bridges the gap caused by single-ladle solutions, making it possible for the casting line to continue operating at full capacity during ladle changes. Additional functions, such as deslagging or the safe, loss-free removal of residual metal from the ladles, can be optionally included.
Metals | Iron, steel, stainless steel, NF metals and aluminium alloys |
Design | Non-heated ladle pouring machine |
Capacity | PUMA PRO pouring machine 1500: up to 1.6 t PUMA PRO pouring machine 3000: up to 3.2 t |
Casting weight | From 8 up to 500 kg with iron and NF-metals; from 12 up to 300 kg with aluminium |
Filling mode | Gravimetric |
Pouring | Flask, flask-less and chemically bonded moulds, and automatic ladling (Al) |
Throughput | Up to 250 moulds per hour |
Downloads
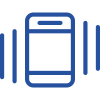
Phone +49 2473 601-710
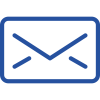
E-Mail info@induga.de