Wegen ihrer hohen elektrothermischen Effizienz und der variabel auslegbaren Geometrie werden Induktions-Rinnenöfen meist für das Schmelzen von Masseln und Ingots, Nichteisen-Metallschrotten und sperrigem Material eingesetzt. Speziell bei der Zugabe von Stückgut oder Ingots zeichnen sie sich durch hohe Temperaturstabilität und Prozesssicherheit aus.
Im Vergleich mit Tiegel-Induktionsöfen ist die Badbewegung sehr gering, sodass an der Oberfläche nur sehr geringe Oxidationen entstehen.
An das hydraulisch kippbare Ofengefäß sind ein oder zwei Rinneninduktoren angeflanscht.
Die Rinnen Induktionsöfen zeichnen sich durch lange Lebensdauer aus, lassen sich sehr leicht reinigen und erfordern nur geringen Wartungsaufwand. In der Kombination mit geringen Energiekosten stehen sie für wirtschaftliches, CO2 freies Schmelzen.
Mit flexiblen Förder- und Hubsystemen lassen sich mehrere Rinnenöfen miteinander kombinieren und an wechselnde Produktionsbedingungen anpassen.
Typische Anwendungen sind das Warmhalten und Vergießen von Metallen, außerdem das Beschichten von Bändern und Stückgut.
Auf einen Blick:
- Flexible Ofengeometrie
- Hoher elektrothermischer Wirkungsgrad
- Kontrollierbare Ofenatmosphäre
- Geringe Betriebskosten
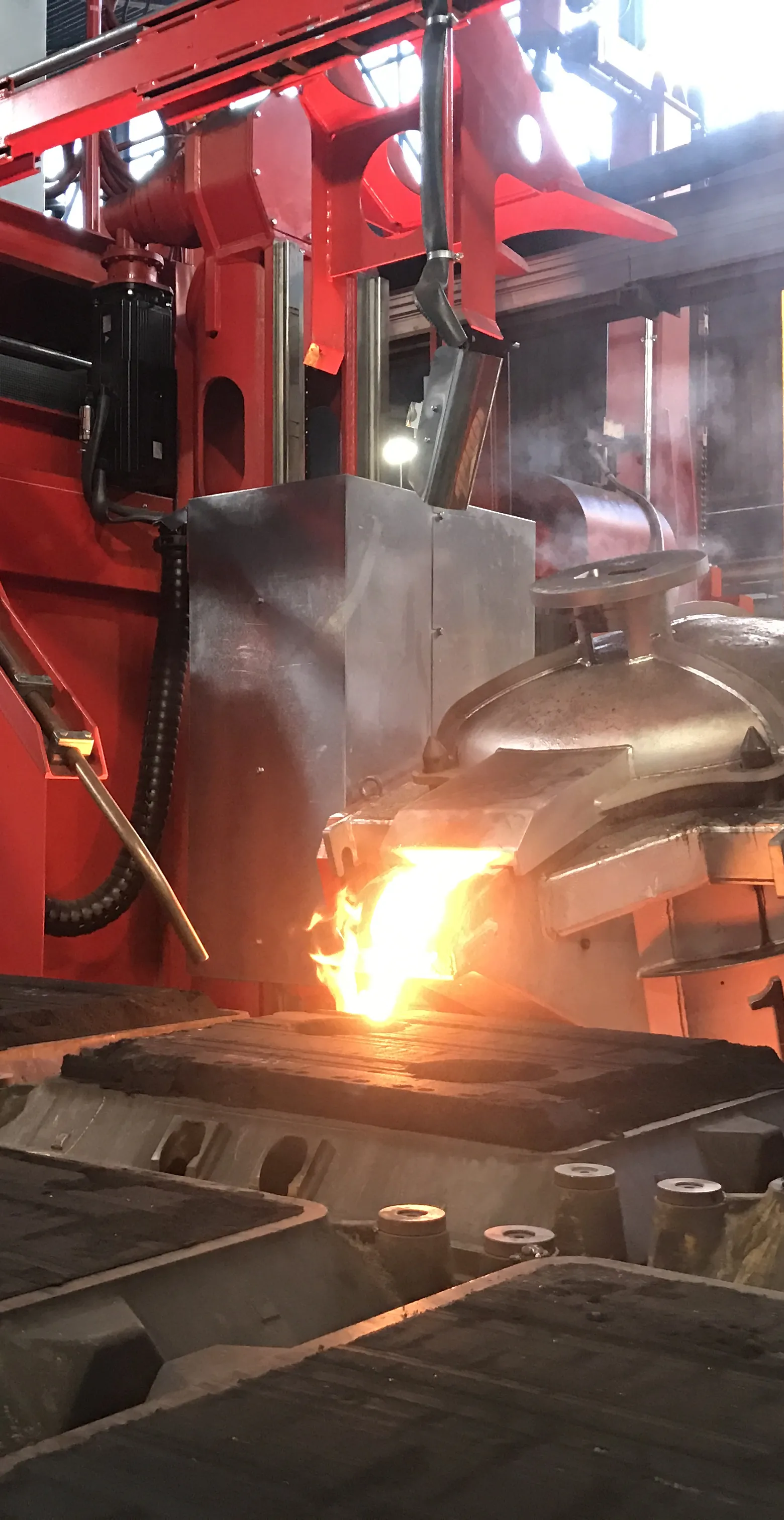
Rinnenöfen: ideal für kontinuierliche Prozesse
Rinnenöfen eignen sich ideal für kontinuierliche Schmelz- und Gießprozesse ohne häufige Legierungswechsel, dabei erzielen sie Wirkungsgrade von 80 bis 90 Prozent.
Der Oberofen, in dem sich die Schmelze befindet, kann wahlweise wannen-, trommel- oder zylinderförmig ausgelegt werden. Auch druckentleerte Mehrkammeröfen können so konzipiert werden.
Typische Anwendung | Schmelzen von Nichteisenmetallen |
Bauart | Rinne mit einem oder zwei Induktoren |
Ofentyp | hydraulisch kippbar |
Elektrische Leistung | 250 bis 3.000 kW |
Fassungsvermögen | 1,0 bis 30,0 t |
Metallentnahme | diskontinuierlich |
Abstichgewicht | 0,6 bis 25 t |
Downloads
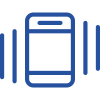
Anrufen +49 2473 601-710
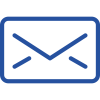
Schreiben info@induga.de